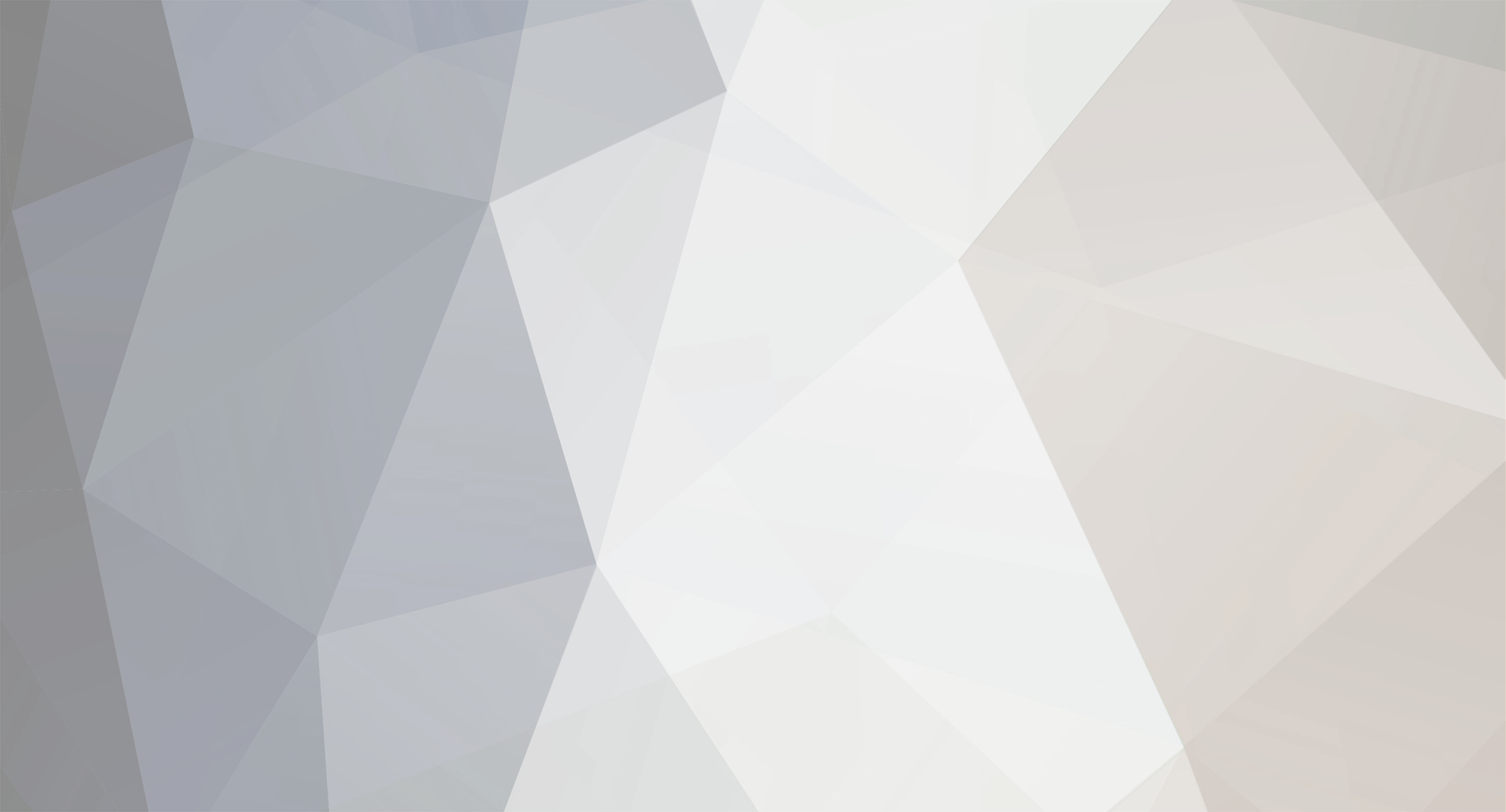
ChefRob
Members-
Posts
45 -
Joined
-
Last visited
-
Days Won
2
Content Type
Profiles
Forums
Latest X-Plane & Community News
Events
Downloads
Store
Everything posted by ChefRob
-
Guessing you didn't make a backup of your 1.0.9 install or save the 1.0.9 installer?
-
-
No problem!!! Thanks
- 7 replies
-
- pocket rocket
- torquesim
-
(and 3 more)
Tagged with:
-
Issue fixed! Hey @Attitude this isn't a @Christoph_T livery... This is my work. If you like you can keep it posted here... Don't mind it at all. But please edit the author of the livery. Thanks ChefRob
- 7 replies
-
- pocket rocket
- torquesim
-
(and 3 more)
Tagged with:
-
Lesson No. 2... Know your aircraft.
-
Have you tried reinstalling the TBM? See if that fixes it. A wav. file is a sound file... Have you tried adding or changing any of those files in the TBM? Do you have some kind of plugin or script that could/would change these?
-
License updated and unexpected gears destruction after landing
ChefRob replied to Erich convair's topic in TBM 900
This could be caused by a hard landing or even a hard turn while taxiing to fast not to mention a few other things. Don't think this had anything to do with it. -
Why would you start a new air frame... That's what the maintenance system is for. I have over 300hrs. on the only air frame I started when I purchased the TBM... I've had not one single issue (outside of normal wear and tear and one admititly hard landing) with my TBM or it's maintenance system yet. What issues are you seeing with it?
-
BetterTBM - Modified Cockpit Textures for Hot Start's TBM-900
ChefRob commented on gjy10's file in General Aviation
- 2 comments
-
- better tbm
- bettertbm
-
(and 3 more)
Tagged with:
-
With the real life GMA 1347A units the "music" button allows you to pipe music from a phone, tablet or MP3 player that you have hooked up using one of the USB ports. As @Goran_M stated it is not modeled in the TBM or any other XP aircraft using the same unit. Just fire up your GoogleMusic, iTunes or what ever streaming service you use... Music in the cockpit.
-
It does state in the manual about setting the (1.) ignition state and to check that the (6.) throttle is in cut off... On page 33 section 5.2 "Initial Cockpit Check" And (4.)fuel introduction is stated on page 35 section 5.5 Here's a great video done by Dasher on the TBM 900 startup.
-
Same as any other LR/G1000 equipped aircraft ".fmc"
-
@2Fat2Fly... It's there and has been from release as far as I remember correctly. When the MFD is powered on and on map mode look in the bottom right hand corner. You'll see three active softkeys... "DCLT-x", "SHW CHRT" and "CHKLST". Click the SHW CHRT softkey and it will bring you to the charts section. From there you just enter in the ICAO code of the airfield(US only) you want to bring up and the G1000 will download it and display it. You can also choose from any available information and a small weather readout as well using a few other softkeys that become active.
-
Good to hear... Beta builds are tagged "Beta" for a reason.
-
I would have to say that this is your issue... Running XP on the most resent 11.34 non beta and see none of this happening. Beta versions are not always the best to run as a everyday setup.
-
That's why you follow a check list... You should actually commit the whole checklist to memory. Then you use the checklist as it should be used, as a check to see that each step was done.
-
Just a friendly little bump... Hoping that @skiselkov sees this and would be able to shed some light on this.
-
No... Totally understand that...110% and ya please just keep out of Saso's way and let him keep working his magic. The magic is strong with him and the TBM. Totally feel you there! I was asking the above because of that... I'm still on the very first airframe I started when I pickup the TBM... Coming up on 200 hours of flight time not including the 20 or so hours that it comes with all ready. I'm using the accelerated maintenance model and outside of a few O2 refills, one or 2 oil top offs, with the last update add GPU costs and I had a fuel pump go bad and I'm around 16k spent. I baby my TBM like I baby my RL C210M. I just wanted to know how the oil wear and tear was modeled/code to manifest itself in the TBM modeling because of how Saso coded it. And how closely he modeled it to the P&Wh PT6's needs. Because by what the P&Wh's manual and service bulletins state the you never really need to change the oil in the PT6's. I'm just interested in knowing how deeply and what parameters the wear and tear on the oil is set. Example... About 5 years ago I had my fuel pump go on my 210... It didn't burn out but a piece sheared itself off inside of the pump itself. Meaning to be safe I needed to have the whole system cleaned out from the pump forward to the engine. So my fuel pump failure was a mechanical one not and electrical type, like say if the pump motor just burned out. Now the systems in a turbine are setup a little different from a piston engine as a turbines oil system isn't for the motor but for the gears and gearbox as far as I understand their workings. So with knowing that I was asking what the wear and tear modeling is based on and how it is implemented in the TBM. We have both the option of topping off the oil and/or changing the oil. So if I assume that Saso has taken into account that both the RL TBM and RL P&Wh maintenance manuals state barring a failure of the cooling system say introducing cooling fluid (which I don't think it can in XP because it look's like the cooling radiator and fluid are not modeled or we would see them in the maintenance manager) into the oil system or dirt (which could be modeled as we can introduce new oil) has some how gotten in the oil... We really shouldn't have to ever change the oil in the TBM. So with this known the question is how is the wear and tear modeled/coded in the TBM... Is it based on hours the oil has on it or is the modeling/coding based on a physical foreign material like dirt or other. I ask cause of how deeply systems are coded and I don't want to be flying along and hit 500 hours on the same airframe in a year only to have the gearbox seize up because I hit a magic number that was coded into the wear and tear modeling/coding.
-
@Goran_M I have a question that's been eating at me lately... It has to do with the maintenance page and the oil. Specifically the oil changing... How is this modeled in the TBM900? In RL life I'v seen numbers as low as every 50 hours of operation and numbers like never you just top it off. I know in a commercially used aircraft that records 100's to 1000's of hours the norm seams to be as long as the engine is on the aircraft and not pulled for maintenance it's just topped off when needed. And the assumption behind this is that even though turbines do burn off oil it is at a lower rate and is less destructive than a piston motor but still enough to be sufficient that the oil maintains much of it's integrity. The only thing could find was the Pratt & Whitney Canada Service Bulletin No. 14001 and it states on page 4 that an oil change is no long a necessity unless it is contaminated by things like transmission fluids, sand and so on. Is this what is being simulated in the HS TBM model? Has HotStart put say an hour rating on the oil to simulate this? Or and I know in real life color is a little important as well... Is this what we should be looking out for and if so... What and how dark of a color should we be looking for? So what are we looking at here in XP... Just wondering.
-
Really couldn't agree more with each comment above... The aircraft is one of the finest in XP, the development team is always on top of their game with updates and assistance in fixing issues or just helping out with the little things. The TBM 900 is not just a great aircraft and product... The HotStart team and the fact that you see that they care about it and it's end users experience with it that really make it stand out. Thanks to the whole HotStart team for bring this product and future products to XP!!!
-
As it is always good to know and understand the math behind everything to do with the performance of the aircraft you are flying. Well... Not good but should be a must. I use either this website or app (both iOS and Android) that is built for the real TBM to use in real life flight planning. They are stand alone apps and not connected to XP in anyway. But I have to tell you it's almost 100% spot on every flight I do with the TBM. Feed in all the information like fuel on board, pax weight start and destination airfields and so on and it spits out a lot of numbers. It even gives you current ATIS for both airfields you enter... Even has everyone of the TBM checklists and so on. It's a really hand app to check out.
-
Wind... Yes of course it will effect how the aircraft handles on the ground depending on wind direction and travel.
-
The G1000 in the TBM is based off of what is offered in the stock LR G1000... With a few more add-ons that HotStart does with plugins. The LR G1000 doesn't have that page in it and HotStart hasn't done a plugin for it... Maybe in the future either LR or HotStart can/will make it happen, time will tell.
-
If as you are saying "it happens with all planes" as well then I have to say you have so settings dealing with your control input settings in XP itself. The latest update to the TBM has tamed it quite nicely. Using the proper taxi techniques and speeds the TBM handles like it's on rails now. I would suggest you also delete/remove that friction script you mentioned in your OP, then reset all of your response curves and set your other control sensitivity settings back to default. And start for there... Outside of tail daggers still being a bit challenging here and there. Ground handling in XP has become a lot better over the last couple of updates.