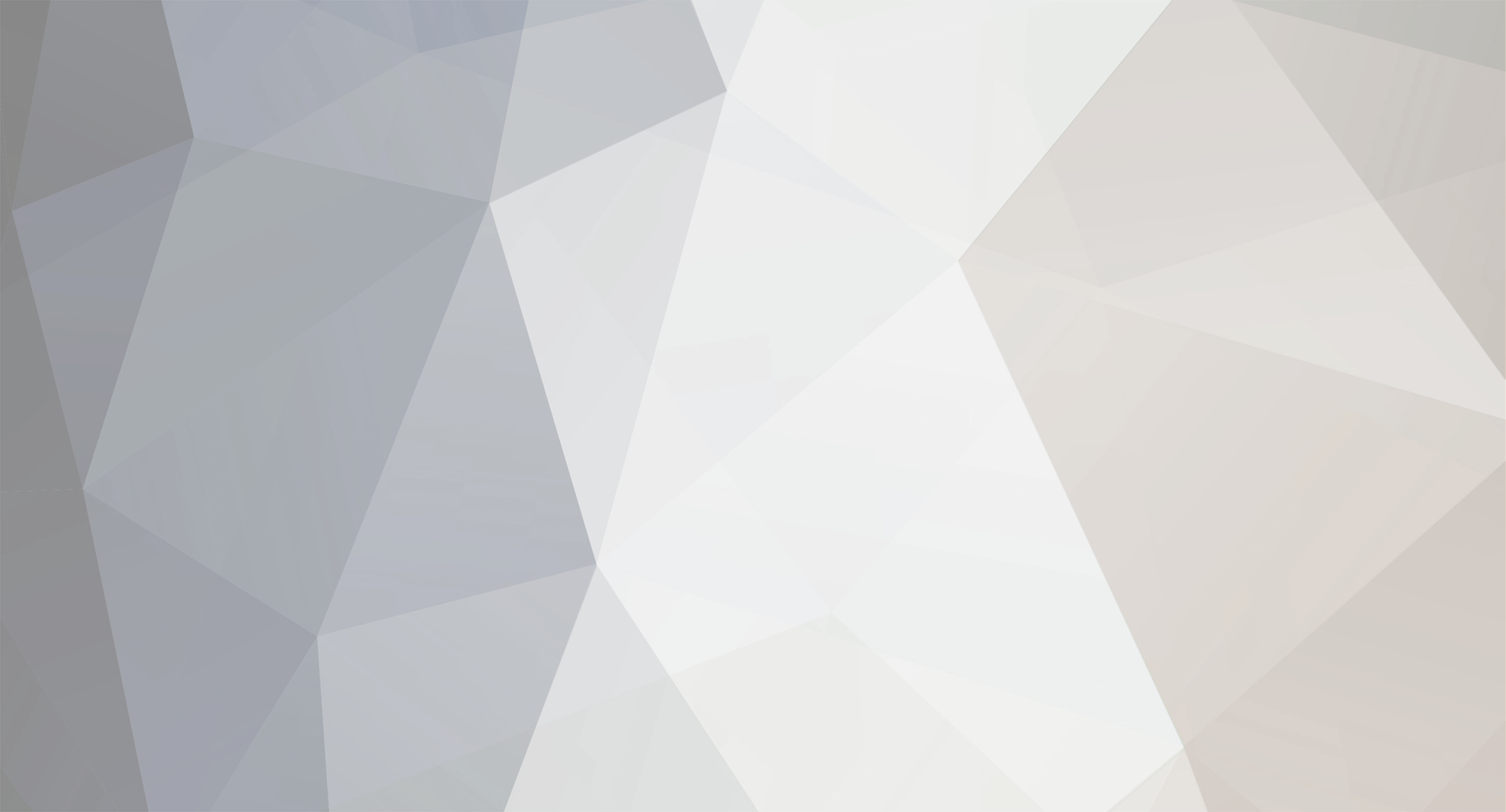
mfor
Members-
Posts
121 -
Joined
-
Last visited
-
Days Won
5
Content Type
Profiles
Forums
Latest X-Plane & Community News
Events
Downloads
Store
Everything posted by mfor
-
That doesn't work for me with IXEGs FMC unfortunately. You can reenter the speed restriction after clearing all restrictions on the legs page of course by leaving the alt parameter blank e.g. 220/
-
Pressing the DEL (delete) button and then the button right to the restriction you want to remove, works for me.
-
Well those numbers refer to the maximum flap speeds - you can deploy the flaps at those speeds if you need the drag, but in most cases you'd deploy them later. As long as you do not bust any speed restriction (ATC or Vspeed) I think it's fine. The FMC target speed on descend is kind of a lower limit, i.e. the AT will increase the throttle if the speed falls below that speed minus 10 knots. You can use the AP in speed/vs mode though to plan your descend manually - which is not unheard of in real life as well, especially since ATC will give you vectors and possibly altitudes that deviate from a preplanned STAR approach every now and then.
-
The mach number is an indicator for the aerodynamic regime you are in. It is expressed as fraction of the speed of sound in the air you are currently surrounded by and for sub sonic flight you'll want to stick below 0.8 or whatever number the manufacturer has set. The speed of sound does not change with pressure , so the mach number does not drop as you increase altitude - it does change somewhat with temperature though. For the 733 it mainly serves as ceiling that you do not want to cross. The true airspeed (TAS) is the speed at which the aircraft is moving relative to the surrounding air and can be calculated from the indicated airspeed IAS and the altitude. It is however not that important to the actual flying, since the behavior of the plane depends on the forces the air exercises, not its actual speed - as long as you don't change the aerodynamic regime. If you go from subsonic to trans/supersonic the forces change dramatically. If you combine the true airspeed with the motion of the air relative to the ground you get the ground speed, which is only important during landing/takeoff and for navigation. These days ground speed is usually provided by GPS. The (calibrated) indicated airspeed (cIAS) is the speed that is displayed on the instruments and derived from the pressure difference between the moving air (at the current speed) and the static pressure. I like to think of the (calibrated) IAS as "aerodynamic speed" because it determines the forces that the flowing air applies to the aircraft, i.e. as the air gets thinner you need to go faster (the true airspeed is higher) for the same amount of force. When it comes to flying this is the most important speed, because it tells you how the aircraft will behave: if it is low you need a large angle of attack too keep the aircraft level and are in danger of stalling if you go slower. If it is high the aircraft will be very responsive to control input and you might exceed the allowed forces of the air frame if you speed up further. The FMC in the 733 will track the IAS setting as long as it does not exceed the selected mach number. So at low altitudes you will be at 280 knots IAS and as you climb higher your true airspeed needs to go up to keep the IAS at 280 as the air gets thinner and at some point you will reach a speed that equals mach 0.72. At this point the FMC will track the mach number instead and basically keep your true airspeed more or less the same (the speed of sound will change with temperature) while the IAS drops as you get higher because the pressure goes down. On descend this is reversed: you will fly at mach 0.72 until the IAS reaches 280 and then the FMC will reduce the TAS during your descent to keep the IAS at 280. Here's a quick table of the corresponding speeds in a standard atmosphere: Altitude IAS TAS Mach Mach TAS IAS 0 280 280 0.42 0.72 476 476 10000 280 323 0.51 0.72 402 460 20000 280 375 0.61 0.72 442 333 30000 280 437 0.74 0.72 424 271 35000 280 473 0.82 0.72 415 242 40000 280 521 0.91 0.72 413 215 To get the ground speed you simply need to add the current winds to your TAS (as vectors). Looking at that table during the climb you aircraft will stay at 280 knots up until roughly FL300 - you TAS/GS will have gone up from 280 to ~437 at that point. (More precisely you'll reach mach 0.72 at 28500 where your TAS is 427.) Climbing further will cause the speed to stay at mach 0.72 and your IAS will drop to 215 at FL400 whereas the TAS/GS will only decrease slightly due to the temperature changes.
-
Simulations hangs after editing some stuff in FMC
mfor replied to Captain_Crow's topic in General Discussion
Unfortunately the current implementation of the editing the route causes rapid creation and execution of new code which any anti virus program will check before execution and this is slowing down the whole sim. As of now the only workaround is to exempt the x-plane folder from live scans in the settings of your AV program. For Windows Defender you can find instructions on how to set up an exclusion at https://support.microsoft.com/en-us/help/4028485/windows-10-add-an-exclusion-to-windows-defender-antivirus- 1 reply
-
- 1
-
-
Well the procedure according to the FCOM is High Altitude Airport Engine Start (above 8400 feet) For airplanes certified for operation at high altitude airports, accomplish the following: Ignition select switch ........................................................................Both Engine start ........................................................................... Accomplish The minimum start pressure is 30 psi minus .5 psi for each 1000 feet above sea level. An indication of N1 rotation plus a minimum of 20% N2 are required prior to introducing fuel to the engine. Engine acceleration will be much slower than during starts at lower altitudes. The engine start switch must be held to the GRD position until N2 RPM reaches 50%. CAUTION: Do not attempt to re-engage the starter above 20% N2 if it is inadvertently allowed to cut out at 46% N2. Note: Fuel fogging from the engine exhaust may occur during a normal high altitude airport start. It also mentions the following limits With APU bleed + electrical load, maximum altitude is 10,000 ft. With APU bleed, maximum altitude is 17,000 ft. With APU electrical load, maximum altitude is 35,000 At SPJJ on ground power I get about 33psi giving me a maximum 21.4% N2 (and 0.4%N1), which should allow an engine start. It might be possible that aircrafts certified for operation at high airports use different N2 thresholds for fuel injection, although when moving the lever to idle a minimal FF is indicated. The IXEG 737 seems to inject fuel at 22.4% N2 (doing cross engine bleed start).
-
IIRC the version is displayed at the bottom of the window that slides in when you move your cursor to the left of the screen. If you've just downloaded it you should have the latest version and you usually get an email if an update is available.
-
Well it's modeling the real world behavior where the spot lights to illuminate the logo are situated in the little tails at the end of the wing. Since the winglets replace those you cannot have both logo lights and winglets at the same time (IRL and IXEG). Also 737-300s leaving the factory did not have winglets and when retrofitting them they (usually?) keep the switches as they were and just stick an INOP sticker on them. So IXEG is following real world practice here.
-
Do you have the IRS systems turned on by chance - that causes a buzzing sound for me. FWIIW you can turn on standby ac power which will feed AC to the left IRS (but drain the battery) and allow you to align it without the buzzer. The right IRS will turn itself off after 5? minutes without AC anyway.
-
It's not about defender: any anti virus program would have to check the executable code the FMC is generating rapidly - so pretty much any virus program should trigger this. For some reason the forums here are moderated in a way to make it look like it's a problem specific to defender, when it really is about how the FMC calculates the routes on the fly, as all virus programs have to check those newly created files for viruses (how else would they know it's safe). So you need to make an exception for this in pretty much any AV program to prevent those freezes from happening, until IXEG can fix things on their end.
-
The pressurization system has 2 (semi) automatic modes of operation: 1) Automatic - you set the FL and the destination altitude and the system will capture the take-off altitude and return to that level on a aborted climb and target the destination altitude for a normal descend. 2) Standby - you set the desired cabin altitude and can also make manual adjustments - this is useful for non standard flights, e.g. touch and go training. There are also two manual modes (AC and DC powered) where you control the opening of the outflow valve manually - this is for emergencies only (e.g. when ditching you'd close the valve manually to prevent flooding and turn off the bleeds to still allow de-pressurization) The flight/ground switch will activate/deactivate the system, however it will also automatically engage when there's no load on the wheels. For normal flights you would use automatic entering FL and destination altitude. I think it's also part of the procedure (may depend on operator) to set the cabin altitude to 200 below field elevation, so in case you quickly need to switch to Standby the plane will be fully de-pressurized when landed (the auto system handles that automatically afaik). As for the bank angle I think I remember someone (Litjan?) saying it should be lower at high speeds, however IIRC LNAV will disregard any limitations to follow the route.
-
solved Take-Off Flaps setting
mfor replied to Dreamliner63's topic in Flight Procedures and Techniques
On Sunday evening it landed at the small Taney County airport, seven miles (11km) away from Branson, Missouri. Passengers on board the Boeing 737-700 reported an abrupt landing as the large plane touched down on the 3,738ft (1,140m) runway. http://www.bbc.com/news/world-us-canada-25717016 Well, they probably needed flaps 15 for takeoff - and a new pair of pants -
mini-EHSI permanent pop-up on demand - SOLUTION!
mfor replied to admroz's topic in General Discussion
Well they kind of have - not on a 737-300 though, I suppose. SCNR -
What you can do though is put the switch in the ground test mode for some time. This will operate the wing anti-ice on the ground. If you do that right before takeoff you can free your wings of ice just long enough for a takeoff and let the normal operation take over once airborne - in heavy icing conditions you might have to go twice through the maximum operating time or even press it while accelerating down the runway. As for running it on the ground - ours is apparently an early model: "Note that on early systems, i.e. those with a GND TEST position, with the WAI switch ON on the ground, the WAI is inhibited until lift-off i.e. 'armed', This is opposite to the present system." http://www.b737.org.uk/iceandrain.htm
-
Take Command! IXEG 737 Classic v1.2 Update Released!
mfor replied to Cameron's topic in General Discussion
AFAIK it was accidentally not included in 1.2 and will hopefully be back with 1.2.1. -
Have you tried disabling the axis and using key binds instead? That would at least confirm that it is a problem with the axis jittering above 0. My guess is that the other planes use different way of handling the axis, e.g. only consider the flaps set if the axis values is greater than say 5% of its value, while IXEG might be using >0. That's just a wild guess though, since I don't know how either product handles this. If that is indeed the problem then maybe you can cheat a bit when calibrating that axis, so that 0 is not fully pulled up - or try one of the tools mentioned in this thread
-
Couldn't you base the trigger for "flaps set" on a different value (if it is currently based on ">0".) for 1.21?
-
Well VNAV is part of the package even though it may get confused at times, which apparently is time consuming to fix (i.e. rewrite) It works well enough for me and I definitely wouldn't want to give up the failure system, immersive sounds, EWGPS/TCAS or the refined flight model for a more feature complete FMC - YMMV of course. Do I wish the update(s) wouldn't take so long? Sure, but as far as I understand it the IXEG team all have "proper" jobs and cannot commit full time to the development. I still feel I got my money's worth out of it, after all it is the aircraft I fly most in XP.
-
centre engine display digital displays not showing 737-300 ixeg
mfor replied to brenden's topic in Hardware/Cockpit Dev
Disappeared as in replaced by by "steam gauges"? There is an option for those in the preferences menu. Edit: Realized just now, you are probably talking about the missing digits No idea why they won't be showing, maybe check for failure settings or some other plugin is causing problems. -
I can't really say how close to the real thing the engines are since I'm not a 737 pilot, however those who are seem to like the flight model. In any case I'd trust the explanations of the developers quite a bit more than some random guy's rants, whose only merit seems to be the ability to look up numbers in planemaker, without knowledge how they are used.
-
Don't know if they are semi accurate - just a two rules of thumb I picked up If you set V/S in feet/min to be about 5 times your ground speed in knots (half the number and add a zero) you'll get an fairly nice 3 (2.8) degree descend and you more or less keep your speed when clean and idle. (e.g. if you're doing 240 knots GS select ~1200ft/m ) for each 1000 feet you want to descend you need about 3.3 miles of space with that 3 degree descend mentioned above, i.e if you need to cross a fix at 10000 and are at 30000, you need to start your descend about 66 miles out - allow some extra miles for slowing down if you need to meet speed restrictions. (feet in 1000s multiply by 3 and add 10%) I use these as guidelines to check what VNAV wants to do and plan longer descends, and for shorter legs I use 1) as starting point for my v/s and adjust according to the "green banana".
-
Well I think level change will always have idle thrust when descending (N1 when climbing) and the AP can just the adjust pitch to meet the desired speed, so the descend rate is determined by the amount of drag you currently have. An Airbus would probably yell at you but the ole 737 just does it The MDH is barometric in that case if I'm not mistaken, so all you do is set the little orange bug at the altimeter - no computer involved there.
-
Try excluding the x-plane folder from live anti virus scans. Apparently what happens is that when you make changes in flight, the route is constantly recalculated and compiled from LUA into executable code which causes the AV to rescan it, slowing things to a crawl - at least that's my understanding as of now.
-
Have you actually tried any of the suggestions in this thread? (test default aircraft, disable plugins, repair/reinstall) People here are usually willing to help, but they can't just wave a magic wand and make your problem go away. It does not seem to be a general problem, because it works for (almost) all people, so we need to find/fix what is different/wrong on your system. And since we cannot access your system, you'll have to do the work I'm afraid.
-
See my edited post. I kind of assumed since you can write the datarefs fairly quickly, they would be updated every frame, but apparently that is not the case. A local variable however should be able to solve the problem of reading the previous (old) value and incrementing it, that is assuming that the function is actually called every (other) time you turn the knob. Edit: You can (and should) add acceleration to that variable as well, or wait until you get your hands on the updated version