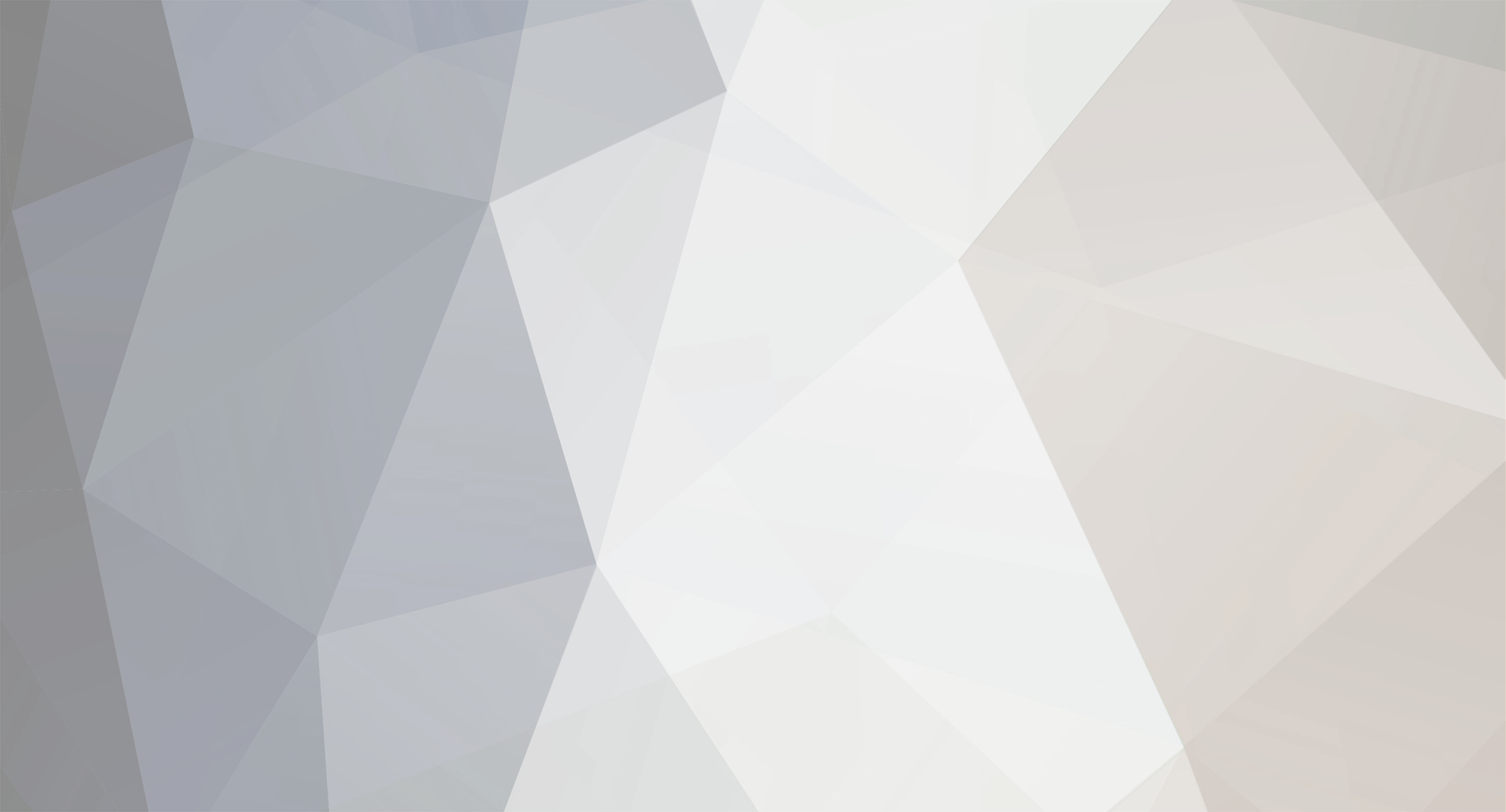
^Wolf^
Members-
Posts
12 -
Joined
-
Last visited
Recent Profile Visitors
1,598 profile views
^Wolf^'s Achievements
Newbie (1/14)
3
Reputation
-
Ahh, correct you are. Optional it is. Interesting article from Saabs Wingtips magazine regarding TAWS. Regulation forced fleetwide implementation of TAWS in the end. Hope I didn't waste too much of your time. Good work on the arcraft guys. ^wolf^
-
All of this is operator specific, the LES guys may have studied/modelled an aircraft that had all the callouts turned off. Many operators in Europe, America, South America and Australia have the 500' call as standard *500' call at 1min 28sec
-
Just a small correction mmerelles, The SF340 does indeed have callouts in real life. Its is a function of the TAWS system, most commonly seen is the Honeywell EGPWS. Depending on the operators requirements/needs/wants it is capable of quite a lot of call outs. Almost all of the following are capable with a honeywell EGPWS 2500, minimums minimums, minimums, approaching minimums, decision height, approaching decision height, 1000, 500, 300, 200, 100, tone alert at 100', 80, 60, 50, 40, tone at 35', 30, 20, 10. The standard callout for every SAAB 340 operator I have seen is the "500" call mmerelles is correct that the Leading Edge Simulations Saab 340 does not have any callouts programed in. ^wolf^
-
@MartinJ I wish there was vertical deviation displayed on the EADI both on this sim and in real world. But even with SAAB 340A aircraft equipped with the Universal (UNS1k) FMS, you will find that vertical deviation is not displayed. Not sure if this is due to integration issues or cost issues or both.
-
Hi Brad, In real world operation once the aircraft passes through 1000' AGL (or another height specified by a specific operator) 1. CTOT- OFF 2. Power Levers reduce to xx% or xxx ITT (Sim purposes initially 80% or ITT below xxx degrees) 3. Condition Levers- Reduce to 1230RPM (Or another RPM specified by a specific operator) Once set, it remains at 1230 RPM for climb, cruise and descent. (You can go condition levers to max if you require Max Continuous Power, or additional drag on descent eg. Emergency Descent- Rapid Depressurisation) Regarding torque settings you need to refer to a climb power chart (perhaps in the LES SF34 documentation). For simplicity you can safely set any torque below 100%, but try to keep the ITT below 830 when below 10,000ft, ITT below 860 above 10,000ft. This is just for good engine care. (^Very similar to real airline operation. ) Condition levers go from 1230 back to max prior to the initial approach fix when configuring for an approach. Keep in mind that all the above depends on specific operators and varies across different continents for different weather/engine/efficiency considerations. Sorry I cant be more specific with my operators procedures. Remember that the LES SF34 documentation is there for specifics and was probably created from real airline ops. Hope I helped, ^Wolf^
-
pots, Regarding the EFIS screens, When the engine driven DC generators are not running (and external power IS connected) when the hydraulic pump activates, all 4 EFIS screens in the aircraft go black. They dim, flash on and off once or twice and red flags for all attitude heading and reference (AHRS) information appear. This occurs because the load required by the hydraulic pump to operate is very large. The ground power unit just does not seem to be able to provide enough power/current for an instantaneous large increase in load. This affects the screens and causes what I mentioned above. While 1 or both engine driven DC generators are running this is not an issue. Just some more info for those curious ^Wolf^
-
Yes, real life SF34 does have Nose Wheel Steering. On the captains side panel there is 'Tiller' to control nose wheel steering. You push down on top of the tiller to electrically activate the nose wheel steering, hydraulics actuate the nose wheel position. If using rudder pedals only on the ground, the nose wheel will castor (move freely). This is why you see the nose wheel changing direction with rudder only. On takeoff the tiller is used until approx. 60-80kts. Tiller is released then rudder is used as it is highly effective for directional control above approx. 60-80kts. Maybe for simplicity of users and/or programming, the Rudder and the Tiller function in Xplane are combined (Maybe only if nose wheel steering is not assigned). I do not know if this is correct or true, someone from LES may provide you with some more information about the specifics of the sim programming and user input. ^Wolf^
-
Hi cruiserdaniels, I also had the same starting issue when I first purchased the Saab 340 software. I found that restarting my computer completely helped on occasion, annoying but sometimes worked. I reinstalled with the latest version and have had no issues. Regarding the pressurisation control panel, When the mode selector on the pressurisation control panel is selected from MAN to AUTO, the fault light should illuminate temporarily (no longer than 3 seconds). This is actually a self test function of the pressurisation computer. If the fault light remains ON the automatic system has an issue. This is where crews would consult the Minimum Equipment List (MEL) book. This would then specify the procedure on how to operate with the system inoperative. In your case is suggest the following, -When selecting MAN to AUTO, check that the fault light illuminates then goes out. If it does not go out, make sure you reset the failures page in Xplane. -If the fault light continues to illuminate, it may be some sort of programming issue that I cannot give any guidance on. -If the fault light goes out as I explained above, next you need to ensure the Manual Pressurisation Control Knob is turned fully counter clockwise. If this knob is anywhere other than this position, a manual pressurisation valve will be partially open, this will cause pressurisation issues eg. Cabin altitude above 10,000ft and/or low cabin differential pressure. Also check that the A knob (altitude knob) is set to your landing airports elevation. If the altitude knob is substantially different to your destination airports elevation, the automatic pressurisation schedule will depressurise incorrectly. In real life this can cause a rapid change in cabin pressure when you land (As the pressurisation valves are driven to open upon landing). Uncomfortable and unsettling for your passengers. Next the B knob (Barometric knob) should just be (for simplicity sake) set and forgotten at 1013hpa/29.92 inches mercury. kneighbour, It depends on the operator which engine is started first. Some operators start the left engine first for exactly the reasons you mentioned. Other operators start the right engine first so the main door with the stairs on the left hand side is always available for evacuation. The only difference is that the guy disconnecting the GPU needs to 'duck' below the tailpipe exhaust so he doesn't get burnt and lose some hair.
-
Hi Charlie, In the real aircraft, Yes it is possible to attempt a takeoff with the condition levers anywhere in the MIN-MAX range. If the condition levers are below the MAX position when the power levers are advanced above the 64 degree power lever angle on the ground, you will get MASTER WARNING-CONFIG, and an intermittent horn that will sound continuously. With the condition levers in the MIN position during takeoff, the propeller blade angle will not be in the most efficient position. This will cause a reduction in takeoff performance. Loose condition levers that haven't had the friction lock set prior to takeoff can vibrate off the MAX position. This causes the CONFIG warning to go off and generally results in a high speed rejected takeoff. This has caused a lot of crews grief over the years. It is important to physically check the condition levers are pushed up to max and the friction lock is set prior to takeoff.
-
Hi there, Regarding the update, I am unable to access it. I am viewing my full invoice on the x-aviation website. On that invoice there is the 'Download links' title Below that it says the following Take Command! Saab 340A Link expires: Sunday 10 August, 2014 3 downloads remaining None of which actually link to anything. It is just light grey text with no link. There is no other link on my invoice to any Take Command! Saab 340 page, website, downloader etc. Your help would be greatly appreciated, Kind regards, Jack
-
Hi all, There may still be some people out there that still have trouble with setting torque, CTOT and achieving Take-Off power (and maintaining during take-off). If you are using a throttle quardrant, such as the one CH Products produces, you may be having trouble because of your throttle quadrant, NOT because of the airacraft program itself. So if you are still having trouble please try the following before raising another thread about CTOT, Torque and not achieving Take-Off power. Possible solutions for you. just try these on the runway with the brakes on and focus on finding out if any of the following are a problem for you Potential Solution No. 1 1. Wind your CTOT to 100% (or desired setting) 2. Physically push you Condition Levers on your quadrant to MAX (Use you hand on your real life quadrant, not a mouse on a screen) 3. Push your Power Levers up to where you would normally set it before turning your CTOT on 4. Turn CTOT on (If not working, keep reading) 5. Gently and slowly retard your condition lever back a few milimeters at a time. (Monitor torque gauges and wait for any response) 6. If CTOT begins to work, stop moving your condition lever backwards. --> Whats happening is X-Plane is not recognising a very small range of you lever position. By moving it backward, the lever now is back in the range that is recognized by X-Plane. By being in the range that is recognized by X-Plane, the CTOT function now knows that it has to send more fuel to the engine. Too far up and CTOT is unable to work out if it needs to send more fuel to the engine. Potential Solution No. 2 1. Wind your CTOT to 100% (or desired setting) 2. Physically push you Condition Levers on your quadrant to MAX (Use you hand on your real life quadrant, not a mouse on a screen) 3. Push your Power Levers up to where you would normally set it before turning your CTOT on 4. Turn CTOT on (If not working, keep reading) 5. Try reducing your power lever. In some cases, up to and possibly more than 20% below the torque setting that is set on the CTOT. 6. Obviously there will be a drop in torque initally, continue reducing vey sowly until you hear the engines spool up --> What could be happening here is confusion between your throttle quardrant and the program. With the power levers too close the CTOT think that it does not need to send more fuel to the engine (as CTOT can only send MORE fuel to the engine). I've found that with CH Products quadrant you may need to set the Power Levers 20% or more below the required CTOT setting for CTOT to engage. Potential Solution No. 3 (CTOT intermittently working) What may be happening is the situation described in "Potential solution No. 1." You may notice at times when you set a lever to a particular position its seems to "wiggle." This is because the potentiometer in the throttle quadrant is between two positions that is determined by the aircraft program. For example the condition lever min-max range may be broken up into 20 individual spots and the computer cant determine weather you're between, lets just say position 15 and 16. so your lever could possibly (I'm not 100% sure) jump between max and the unknown range as described above. All of the above is for PHYSICAL throttle quadrants that people have bought and plugged into their computer. I have a CH Products Throttle Quadrant and I found that the above solutions to work for me. Could be just me. Could help someone now or in the future. Perhaps good knowledge for the makers and support team of the SAAB. Safe Skies